Separation
Precise Separation. Customized Solutions
Introduction
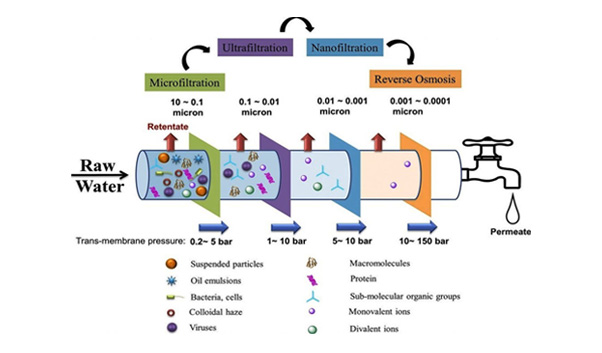
Separation is the conversion of a mixture of substances into two or more distinct product mixtures. During a separation process, at least one of the constituents in the source mixture is concentrated in the final result. Sometimes, a separation process can completely divide the mixture into its pure components. Also, purification is a specific type of separation process where we can separate and isolate a desired component from a mixture of components. Importantly, separation of a mixture can exploit the differences in chemical and physical properties between the constituents of the mixture.
Moreover, separation processes are often classified according to the particular differences that the processes used for the achievement of the expected separated products. However, if there are no specific differences between the constituents in the mixture, we may have to use multiple operations in combination with each other to get the desired end product.
Generally, chemical elements and most of the compounds occur in the impure state in nature. Therefore, we can separate the desired elements or compounds from their source (ore) and perform a separation process before the constituents can be put into productive use. Thus, this makes the separation techniques essential for modern industry.
Providing Separation process solutions and Systems by using of process Membranes Technologies and our deliverable Products are:
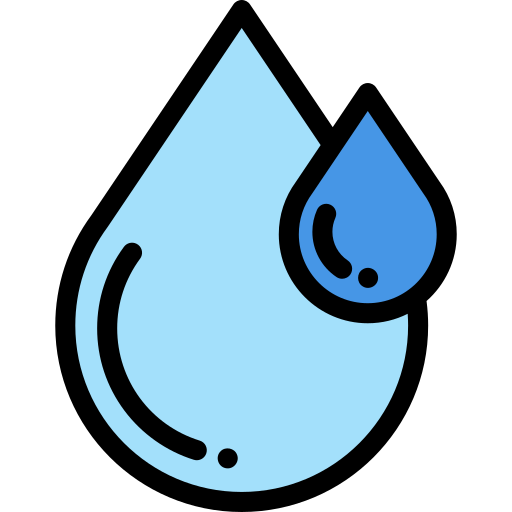
Reverse Osmosis System
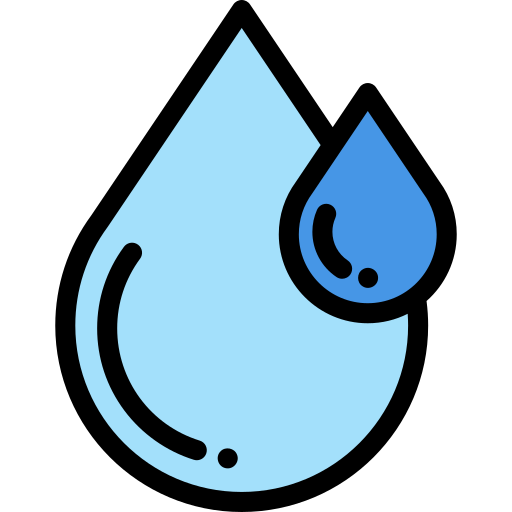
Ultrafiltration System
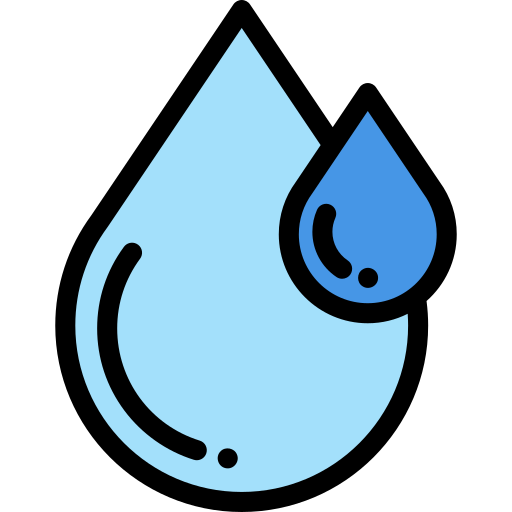
Ion Exchange Plants
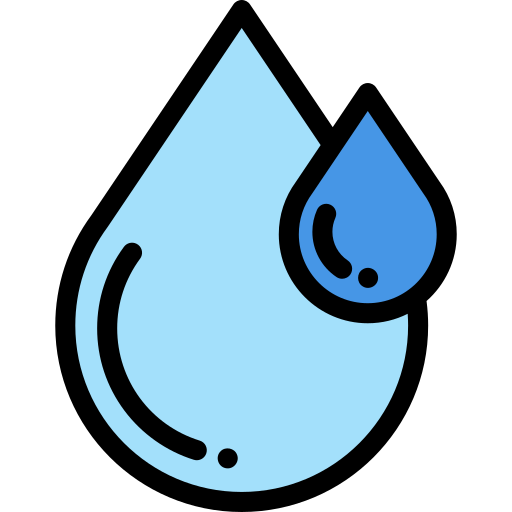
Forward Osmosis Systems
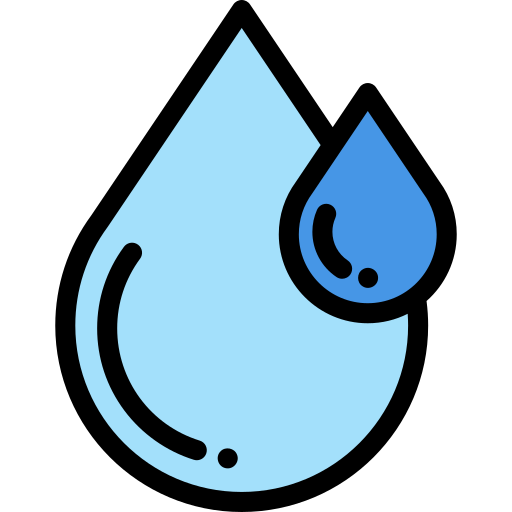
Nanofiltration System
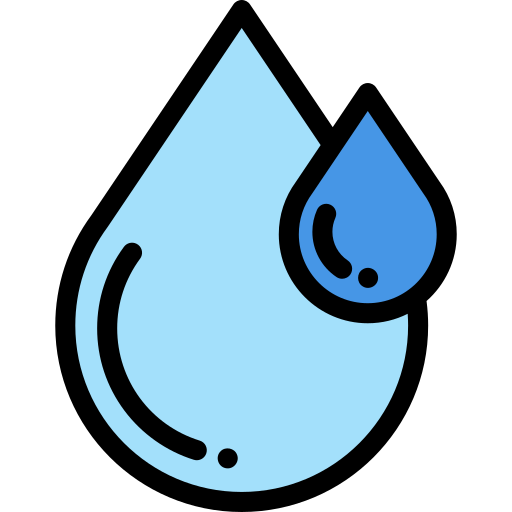
Microfiltration System
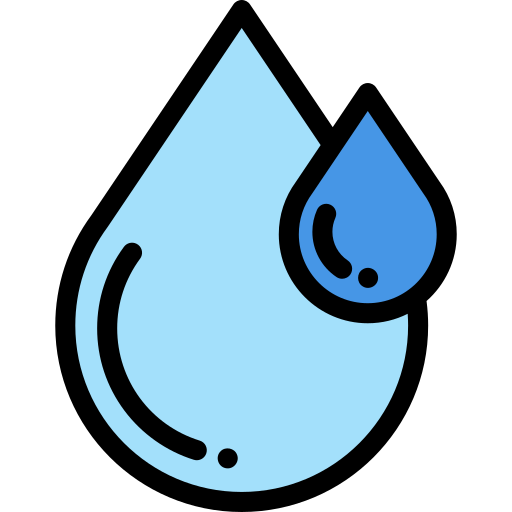
Ceramic Membranes Systems
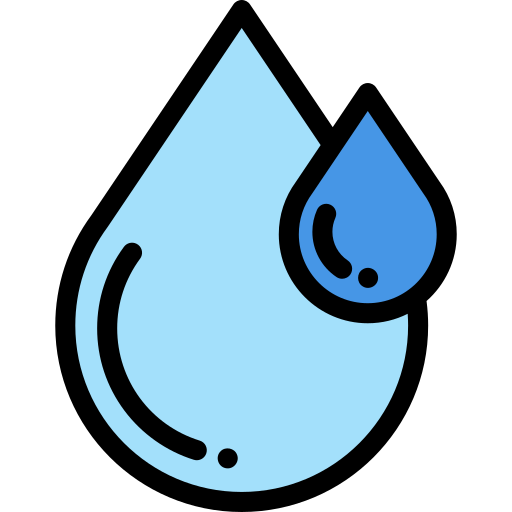
Piloting Plant for various process fluid & product
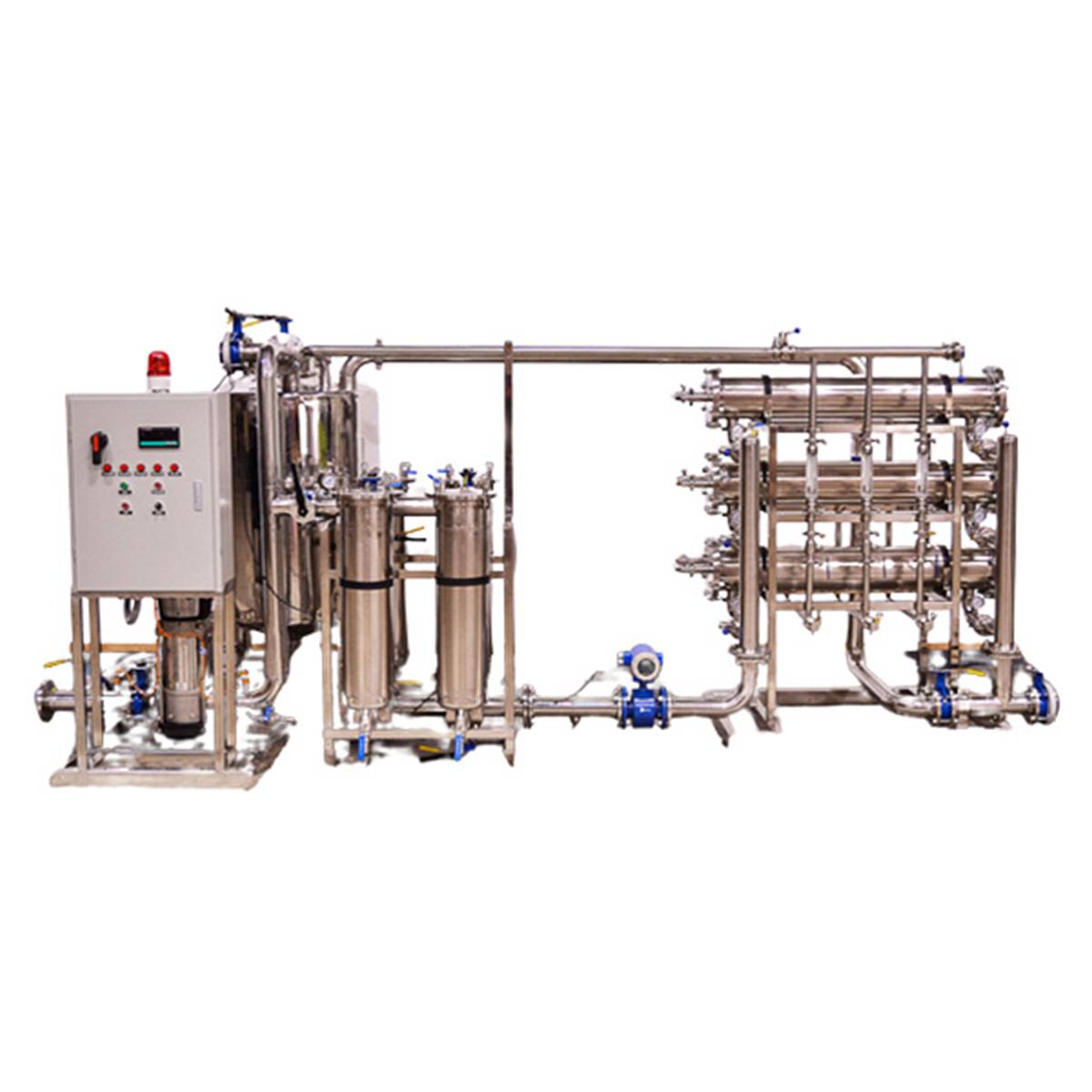
WFI RO Plant
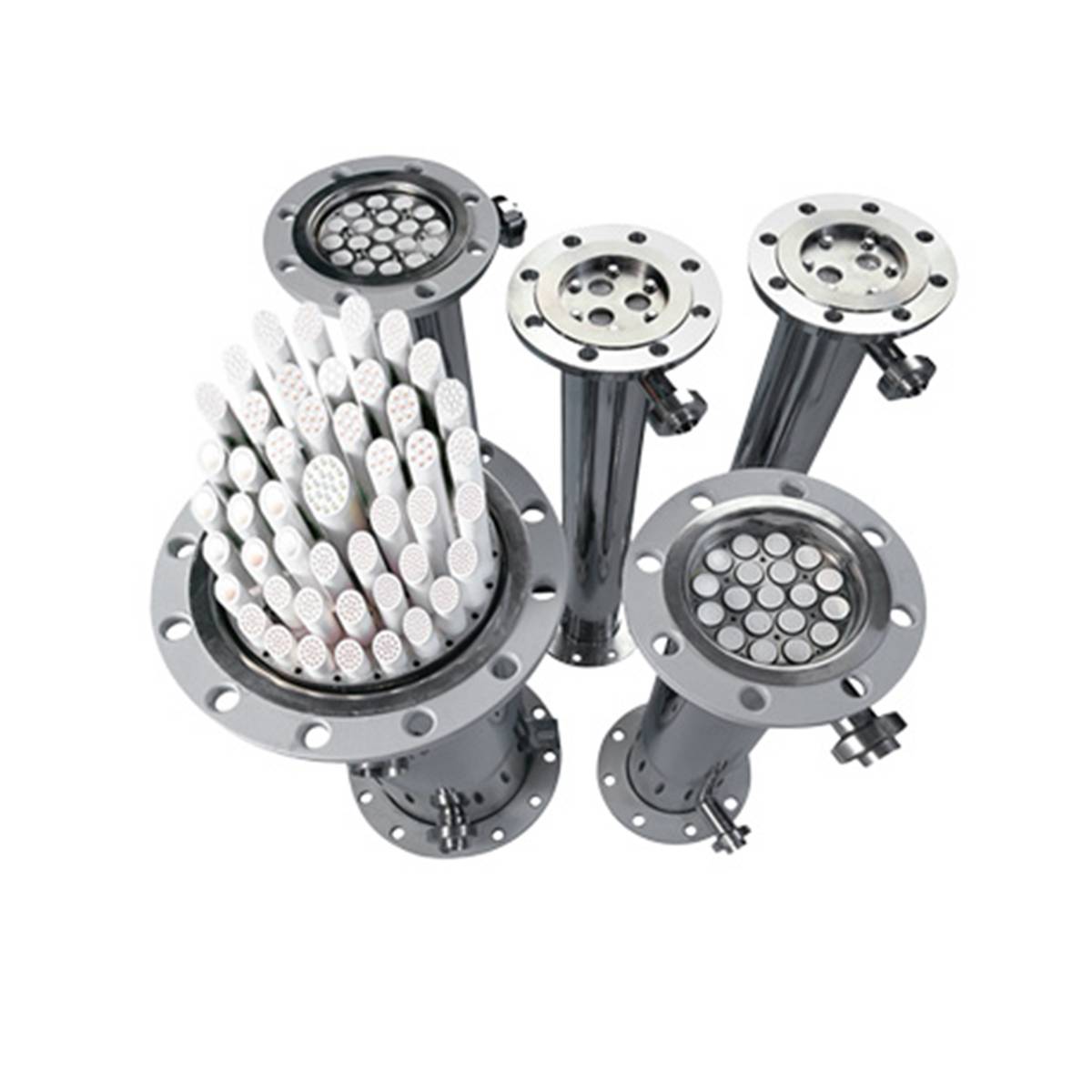
Ceramic Membranes
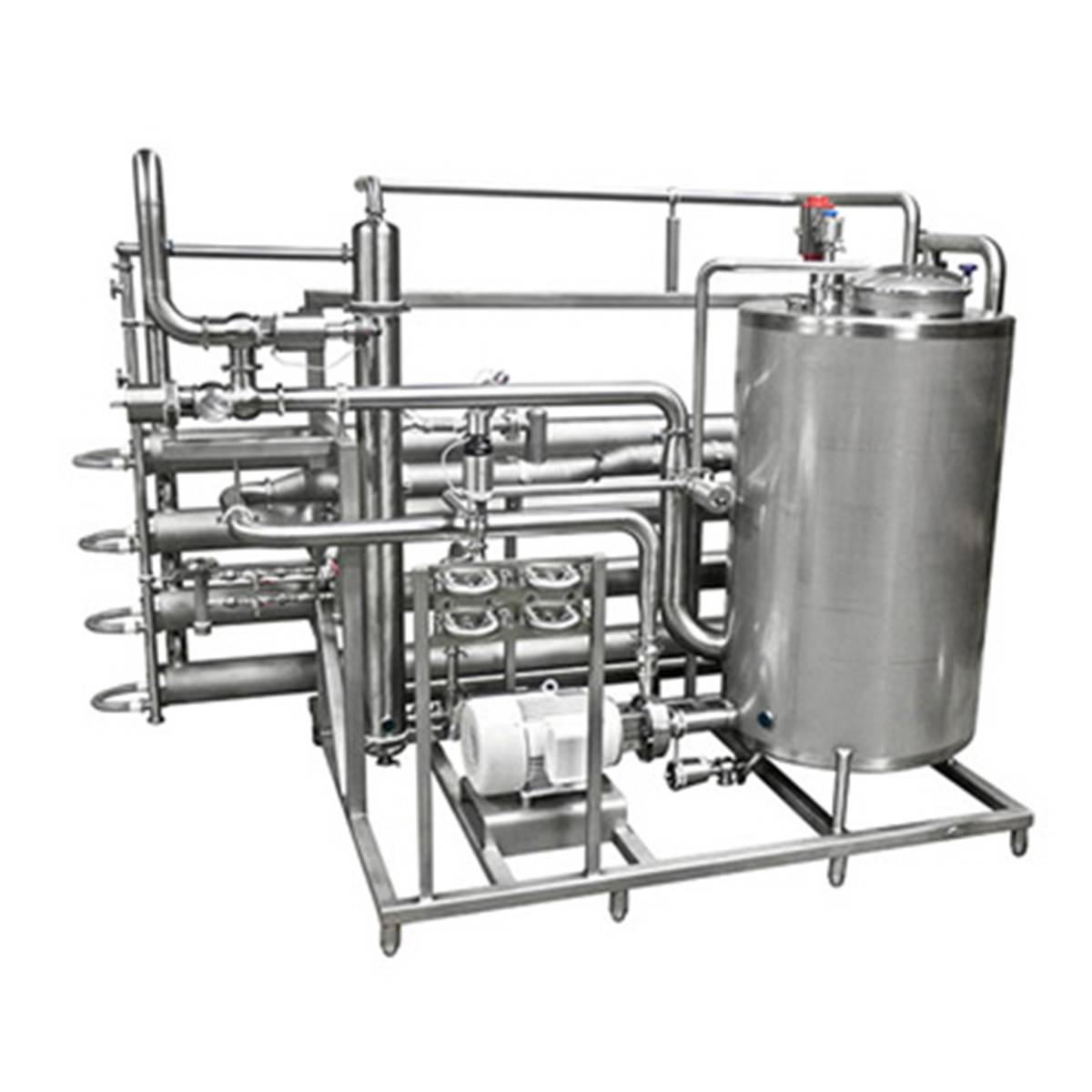
Caustic Recovery NF Membrane Plant
In Our
Manufacturing
We are manufacture of following Lab scale and Pilot scale separation and green energy related products for Research/Academic Institutions and all type of Industries. We offer a range of services, including installation, maintenance, and technical support.
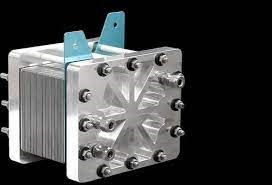
Hydrogen Fuel Cell Stacks Technologies
Hydrogen fuel cell stacks are at the core of hydrogen fuel cell technology, which converts chemical energy from hydrogen and oxygen into electrical energy through an electrochemical reaction. Fuel cell stacks consist of multiple individual fuel cells connected in series and parallel to meet specific power and voltage requirements.
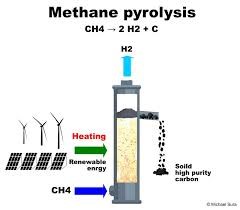
Methane Pyrolysis to Green Hydrogen Production
Methane pyrolysis is a process that involves the thermal decomposition of methane (CH₄) into its constituent elements, carbon (C) and hydrogen (H₂), without the direct use of oxygen. This process is a potential method for green hydrogen production because it avoids the formation of carbon dioxide (CO₂) during the hydrogen production stage, making it a cleaner alternative to traditional methane reforming processes.
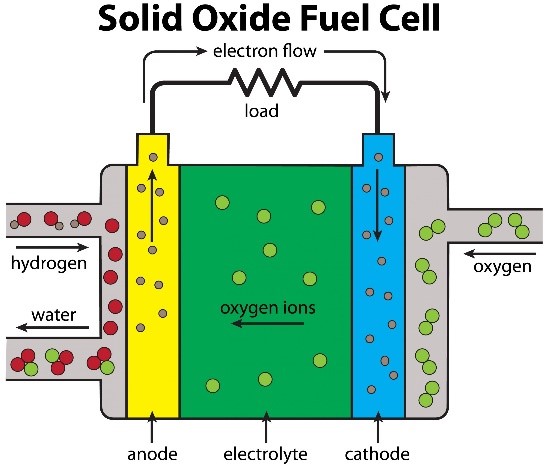
Solid Oxide Fuel Cells (SOFC)
Solid Oxide Fuel Cells (SOFCs) are a type of fuel cell that electrochemically converts chemical energy directly into electrical energy using an oxidizing agent and a fuel source. Unlike other fuel cells, SOFCs use a solid oxide or ceramic electrolyte to conduct ions, typically oxygen ions (O²⁻).
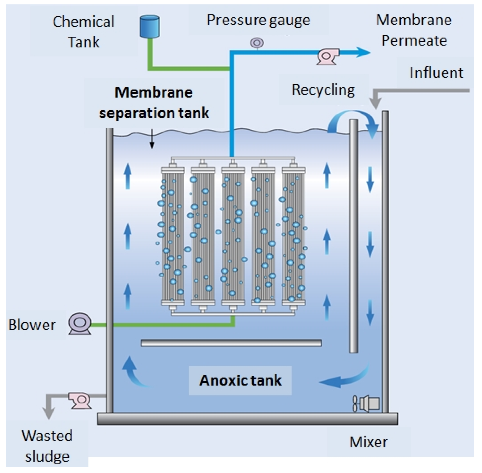
Membrane bioreactor system (Submerged and Side Stream)
A Membrane Bioreactor (MBR) system is a technology used in wastewater treatment that combines biological treatment with membrane filtration. This technology offers advantages over conventional wastewater treatment processes by providing high-quality effluent in a more compact and efficient system. Advantages of the MBR system includes High-Quality Effluent, Space Efficiency, Flexible Design, Reduced Sludge Production.
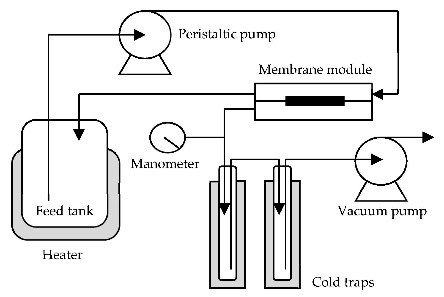
Pervaporation (PV) System (Available with Polymeric and Ceramic Membrane Modules)
Pervaporation is a membrane separation process that involves the selective permeation of one or more components of a liquid mixture through a membrane. The process takes advantage of the vapor pressure difference between the feed liquid mixture and the permeate side, allowing for the preferential transport of certain components through the membrane. Pervaporation is often used for the separation of liquid mixtures, especially those with azeotropic compositions or those that are difficult to separate using conventional methods.

Forward Osmosis (FO) System
Forward Osmosis (FO) is a membrane separation process that involves the natural movement of water through a semi-permeable membrane from a region of lower solute concentration (the feed solution) to a region of higher solute concentration (the draw solution). This process is driven by the osmotic pressure gradient across the membrane. FO is distinct from reverse osmosis, where water is forced through the membrane against its natural osmotic flow.

Gas Separation System
A gas separation system is designed to separate different components or impurities from a gas mixture, typically by using specialized membranes or other separation techniques. Gas separation plays a crucial role in various industrial processes, including air separation, natural gas processing, hydrogen purification, and more. Different methods are employed depending on the specific requirements of the application.
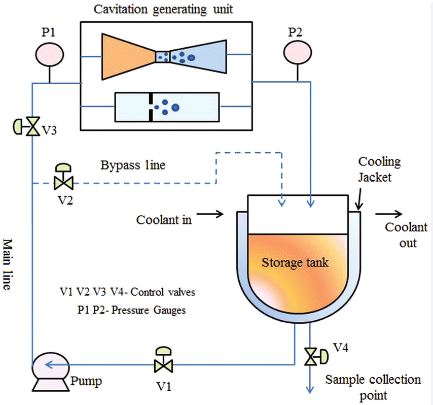
Hydrodynamic Cavitation Reactor (HCR) With Ceramic and Polymeric Membranes
A Hydrodynamic Cavitation Reactor (HCR) is a device designed to induce hydrodynamic cavitation—a process in which high-speed fluid flow generates localized low-pressure zones, leading to the formation and subsequent collapse of vapor-filled cavities within the liquid. This phenomenon results in intense physical and chemical effects, including high temperatures and pressures, shock waves, and the generation of free radicals. Hydrodynamic cavitation can be utilized in various applications, including chemical processing, water treatment, and biodiesel production.
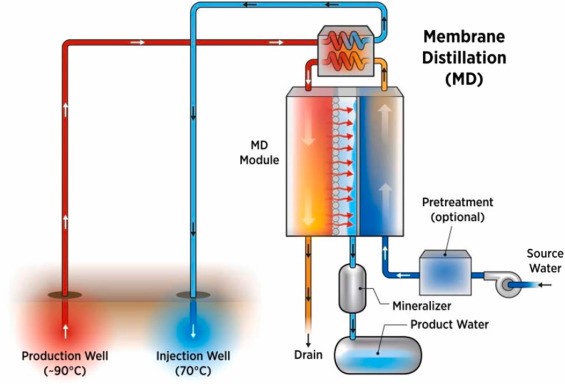
Membrane Distillation (VMD, MDC, AGMD)
Membrane distillation (MD) is a separation process that utilizes a hydrophobic membrane to allow the selective passage of water vapor through it, while preventing the passage of liquid water. This process is driven by a vapor pressure difference across the membrane, typically created by a temperature gradient. Membrane distillation is particularly useful for desalination, wastewater treatment, and concentration of solutions.
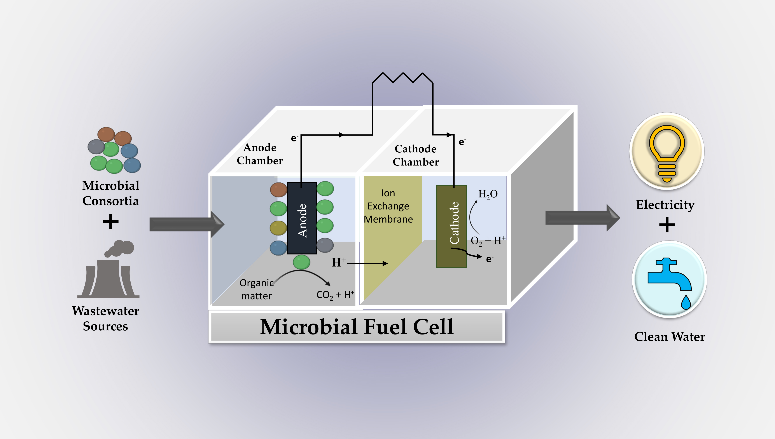
Microbial Fuel Cell (MFC)
A Microbial Fuel Cell (MFC) is a bio electrochemical device that converts the chemical energy stored in organic matter, such as wastewater or organic substrates, directly into electrical energy through the metabolic activities of microorganisms. MFCs have gained attention as a sustainable and eco-friendly technology with potential applications in wastewater treatment, power generation, and environmental monitoring.
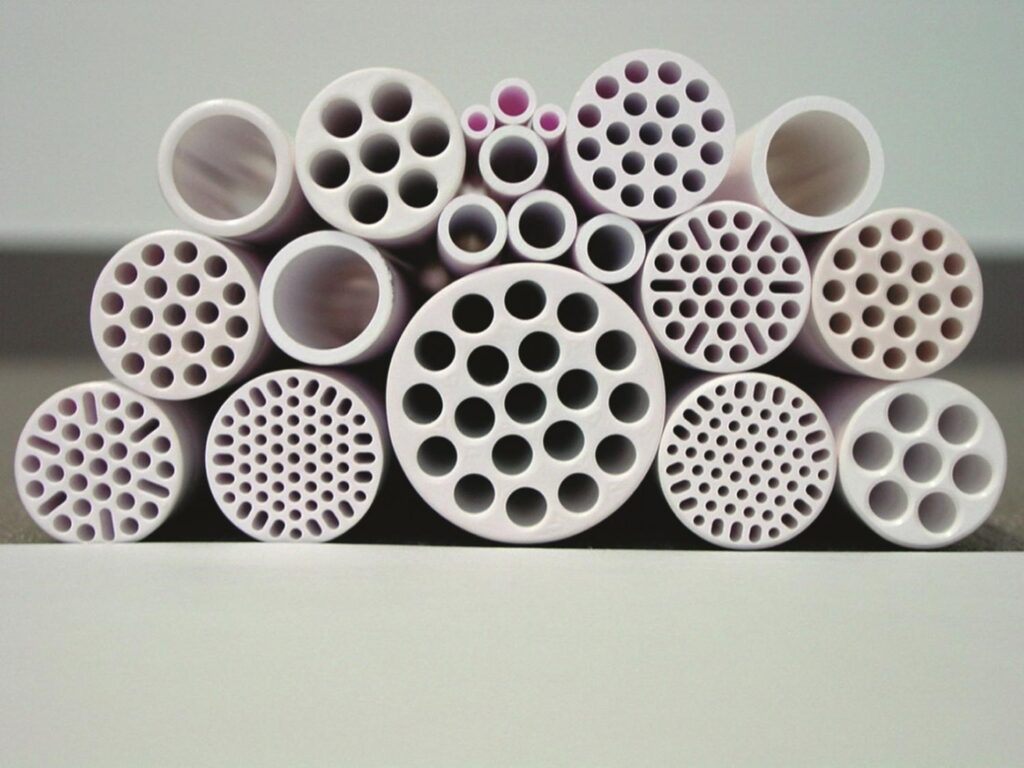
Ceramic Membranes with different micron size (Single and Multichannel Configuration)
Ceramic membranes are a type of filtration technology that uses ceramic materials with specific porosity and structure to separate particles or molecules from a fluid. These membranes are known for their durability, thermal stability, and chemical resistance. The micron size and diameter of ceramic membranes can be tailored to meet the requirements of various applications.
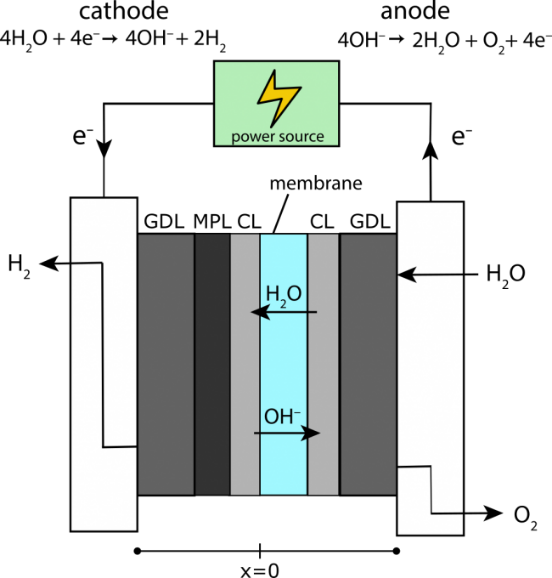
AEM Electrolyzer System
AEM (Anion Exchange Membrane) electrolyzer systems are devices that use electrochemical processes to split water into hydrogen and oxygen gases. Electrolysis is a key technology for the production of green hydrogen, which can be used as a clean and renewable energy carrier.
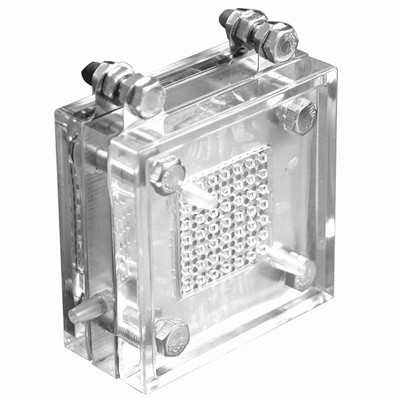
Proton Exchange Membrane Fuel Cell
A Proton Exchange Membrane (PEM) fuel cell is a type of electrochemical cell that converts chemical energy from hydrogen fuel directly into electrical energy through an electrochemical reaction. PEM fuel cells are particularly attractive for various applications due to their efficiency, high power density, and low-temperature operation.
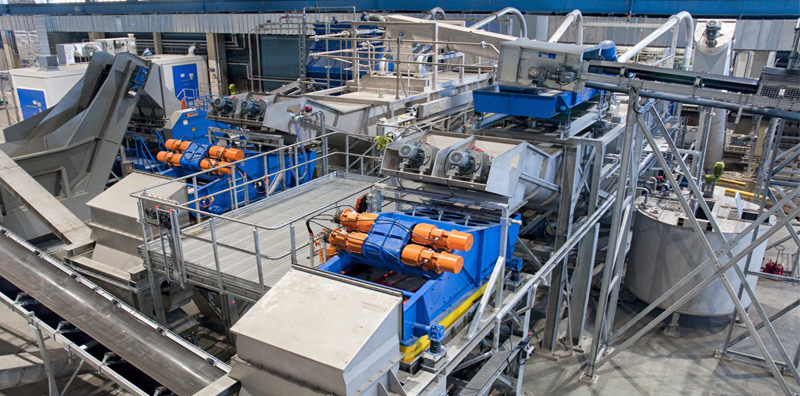
Separation, as a comprehensive scientific discipline, constitutes the art of isolating specific constituents from complex mixtures. This all-encompassing field encompasses an array of techniques, each tailored to the distinctive properties of the substances being separated.
Environmental Remediation
Moreover, separation techniques are indispensable in environmental remediation, where contaminated soils and waters are subjected to purification. These processes are pivotal in mitigating environmental risks and ensuring that natural resources are preserved for future generations
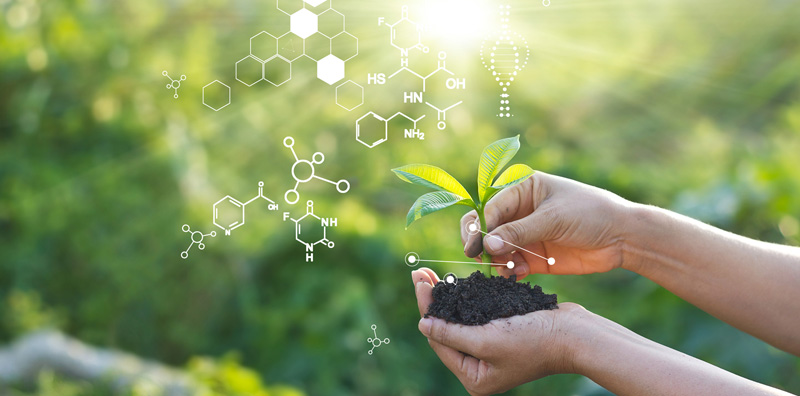
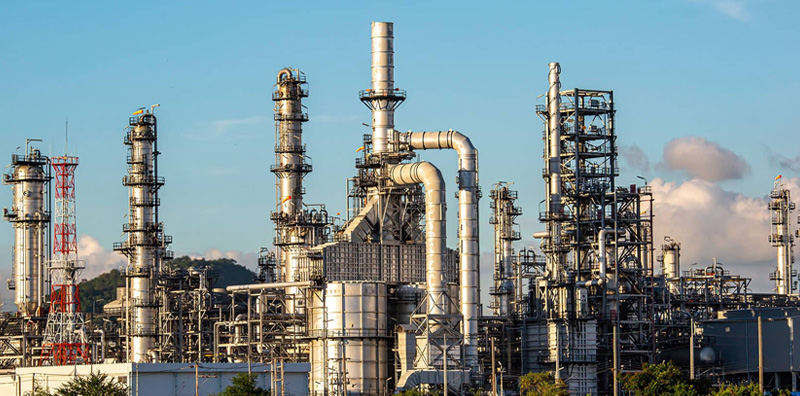
Industrial Significance
The industrial significance of separation processes is profound & pervasive. In the realm of petrochemicals, separation methods are the lynchpin of the refining process, where crude oil is meticulously transformed into an array of valuable products, from gasoline to petrochemical feedstock. Within the food processing industry, separation is paramount in the extraction of pure constituents from raw materials, ensuring the safety & quality of food products.